Sweden’s clear focus, from fibre to fashion
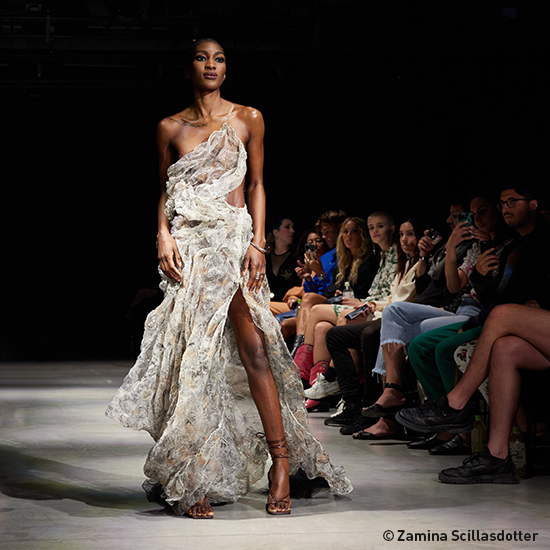
16 22
September 2027
Messegelaende HannoverGermany
The 2020s are already proving to be a time of very significant change and technical textiles will provide key solutions addressing some of society’s biggest challenges going forward – and particularly in respect of sustainable products that will contribute to the wider issue of combatting climate change.
Since June 2020 – with the Covid-19 pandemic having suspended the regular international conferences and exhibitions that are so vital to the exchange of new ideas – the textile machinery branch of the VDMA has held no less than 29 webtalks, most of them dedicated not only to individual technology challenges but also to in-depth solutions across the value chain.
These have covered aspects of sustainability ranging from recycling and new, minimal application dyeing and finishing processes to textile reinforced concrete as the future of sustainable building and have been joined by 4,700 specialists from around the world.
For many years here in Germany, the textile machinery companies of the VDMA – working closely in a synchronised network of allied industries along the supply chain and many research institutes – have been on a mission to explore every avenue of the potential for advanced textiles.
The VDMA has members producing technologies for every stage of production – from fibres and filaments through the consolidation processes of yarn spinning, weaving, knitting, braiding and multiple nonwoven bonding routes, and on to all aspects of dyeing, finishing and coating. The ongoing digitalisation of all textile technologies is yielding major benefits in terms of efficiencies.
When it comes to end-use applications, I can think of many fields in which technical textiles will be instrumental in making major sustainable advances, but here, let me name just three – construction, electric vehicles and energy generation.
Around 10% of the world’s carbon emissions are generated by construction, and the use of composite reinforcements in structures is already widespread. A major emerging field is that of textile-reinforced concrete.
Researchers at the Technical University of Dresden and industry partners, for example, have been working with architecture firm Henn to create the first concrete building to be reinforced with carbon fibres instead of steel – The Cube.
Carbon yarns are used to create a mesh that the concrete is poured onto and the resulting material is four times stronger than regular concrete, but also four times lighter, due to the reduced structural sections.
The carbon-fibre mesh is also rust-proof, unlike steel, meaning carbon concrete has a longer lifespan and can be much thinner, since much of the thickness of steel-reinforced concrete is due to the need to prevent water penetration leading to oxidisation of the rebar.
The Cube is a showpiece for a major TU Dresden research project called C³ – Carbon Concrete Composite – which is backed by the German Federal Ministry of Education and Research.
Technical textiles have proved invaluable in shedding the weight of today’s cars through the replacement of heavier materials, while also contributing to both engine efficiency and clean cabin air. A lot is now happening in electric vehicles, in both components and battery technologies.
Ongoing research programmes involving VDMA textile machinery companies have led to many new products for electric vehicles, ranging from battery separators and gas diffusion layers to battery housings and even filters for the removal of harmful brake dust.
Another big use for glass-fibre textile reinforcements is meanwhile to be found in the panels of the electric delivery vehicle fleets which are being built to deal with the explosion in internet shopping.
Energy represents 27% of all emissions and we know that the move to renewables is going to accelerate over the next few years.
Technical textiles are already embedded in the renewable energy sector with glass and carbon fibre reinforcement extensively used in turbine blades and nacelles.
Offshore wind power generation is becoming more efficient and cost effective all the time and a key to it is the longer wind turbine blades that are now being manufactured. In 2020, LM Wind Power in France unveiled what is currently the world’s longest wind turbine blade at 107 metres. For context, the length of a football pitch is 105 metres.
With the cost of energy having already escalated to unprecedented levels even prior to the beginning of the tragic war in Ukraine this February, an intense international examination of global energy sources and supply chains has been underway.
Germany’s dependence on Russian gas has made headlines, but did you know that also in February this year, the country generated a record 20.6 terawatt-hours of wind energy, which made up 45% of its total energy?
There are also recent developments using natural fibre composites in turbine blades or nacelles, including those produced in Germany by a company called Greenboats.
Technical textiles will play a key part in other components, whether through pultrusion to manufacture cylinders or membrane technologies used in the production of green hydrogen, with other applications still to be commercialised.
At ITMA 2023, visitors will discover not only a wealth of often surprising applications for today’s technical textiles but in particular, the increasingly sophisticated technologies behind their production. The show will also underline their multi-faceted contribution to a sustainable future.
Thomas Waldmann, Managing Director, VDMA Textile Machinery Association
About VDMA Textile Machinery Association
The VDMA Textile Machinery Association represents a powerful branch of European mechanical engineering, with around 130 member companies – many of them world market leaders – in technologies ranging from spinning to finishing.
Subscribe to our mailing list and stay up-to-date with news and developments in ITMA and the textile and garment industry.