Working with customers closely on tailor-made solutions
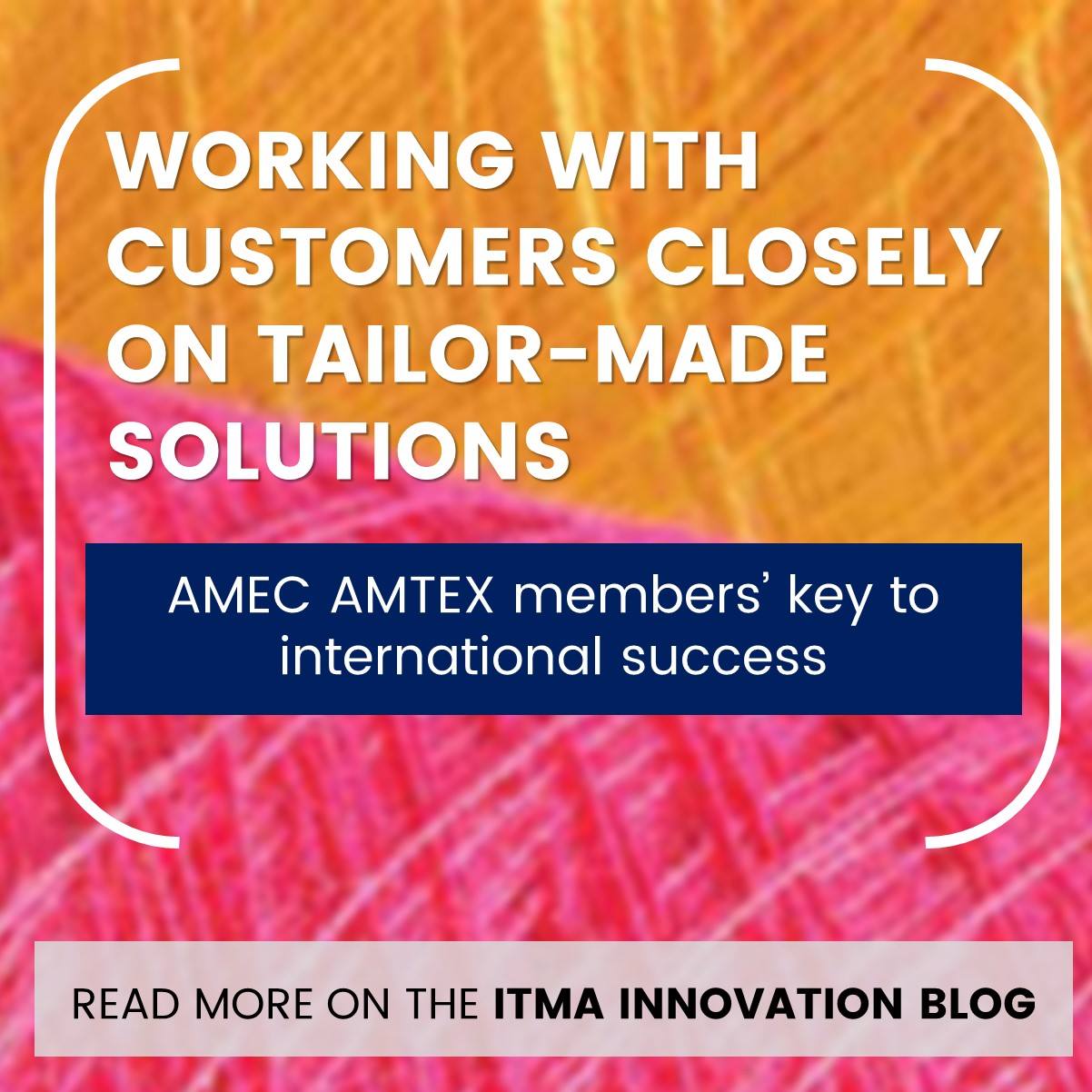
16 22
September 2027
Messegelaende HannoverGermany
The scale of the work undertaken by the manufacturers of textile dyes and chemicals to be in compliance with the European Union’s REACH regulations is nothing short of breathtaking.
REACH – Registration, Evaluation, Authorization and Restriction of Chemicals – mandates that listed chemical substances manufactured and marketed into the EU have to be registered with the new European Chemicals Agency (ECHA) in Helsinki.
It has been introduced in phases, with a first deadline in 2010, a second in 2013 and a third which took effect from June 2018.
The third phase applies to all listed chemical substances manufactured and marketed into the EU in quantities of over 1 ton (1,000 kg) and as such, has required significantly greater attention than the previous two phases.
Even for the major global manufacturers of differentiated textile dyes and chemicals – including Archroma, DyStar and Huntsman Textile Effects, who are all leading ITMA exhibitors – the task has proved daunting.
Archoma says it has made an investment of some US$14.5 million to register just 135 substances for this third phase of REACH, and DyStar estimates it has cost the industry in total around €2 billion in additional tests and the production of over 80,000 new registration documents.
According to Huntsman, 20,723 registration dossiers for substances were submitted to ECHA by the 2010 deadline, covering 3,400 substances and a further 9,084 registration dossiers were submitted by the 2013 deadline, covering a further 3,000 substances.
In the beginning we started with the registration of some rather big volume items, but at the end, the handling of dozens of small but nevertheless important items all needed to be managed in parallel,” says Dr Clemens Grund, Dystar’s senior director of global technology and ecology, adding that the workload at the testing institutes was very challenging and the ECHA now expects the dossiers to be regularly updated at six-month intervals.
Since the beginning of REACH, much European production of dyes and chemicals has migrated to Asia, but the EU has set a benchmark that is now being copied elsewhere.
Turkey, for example, introduced its own REACH-like legislation in 2017, representing a further challenge for the globalised manufacturers. China, India and South Korea are also planning similar programmes.
In China, over 100 dyeing and finishing plants have already been closed down in the past three years as a result of stricter new environmental regulations and an estimated 1,400 are being made to comply with much tougher standards and to adopt new sustainable technologies, including cleaner dyes and chemicals.
Currently, much higher prices are being commanded for many dyes and chemicals, as well as shortages of certain key ingredients for formulating them, as the global market adjusts to these new circumstances, with smaller dye producers in particular, reporting operational difficulties.
The willingness of the market leaders to innovate with sustainable new products, however, remains undimmed.
Archroma, for example, has been promoting its Advanced Denim dyeing technology which allows savings of up to 92% in water, 87% in cotton waste and 30% in energy, compared to a conventional denim dyeing process.
Archroma’s EarthColors technology turns non-edible waste products into new dyes. | Photo credit: Archroma
Its EarthColors technology meanwhile promotes the concept of 100% traceable dyes which are from non-edible waste products that have been collected from the agriculture and herbal industries. These plant-based dyes are sourced from up to 100% renewable resources.
Earlier this year, the Dutch brand G-Star Raw launched the world’s first Cradle to Cradle (C2C) Gold level certified denims by partnering with Dystar denim manufacturer Artistic Milliners. These denim fabrics are based on the cleanest indigo technology ever to be formulated, using 70% fewer chemicals, no salts and producing no salt by-product during the reduction and dyeing process, consequently saving water and leaving clean and recyclable water effluent.
Dystar has helped denim manufacturer G-Star to launch the most eco-friendly denim jeans to date.
Among the latest products from Huntsman Textile Effects is Phobotex RSY which raises the bar in the field of non-fluorinated durable water repellents (DWRs). This new product is allowing brands and retailers to meet global demand for eco-friendly clothing requiring extreme rain and stain protection. The industry continues to shift away from traditional formulations based on perfluorinated chemicals (PFCs) due to environmental health and safety concerns.
Phobotex RSY from Huntsman Textile Effects raises the bar in the field of non-fluorinated durable water repellents (DWRs).
Further sustainable innovations will be detailed at the 3rd Textile Colourant and Chemical Leaders Forum which will be held alongside the next ITMA on June 23 2019. The forum’s theme is The Circular Economy and Resource Sustainability Strategy.
Discussions will centre on the circular economy and resource sustainability strategy and how textile chemicals and innovative and cleaner technologies can support it under the influence of Industry 4.0 as an emerging strategic concept,” says Andrew Filarowski, chairman of the forum’s organising committee and technical director of the Society of Dyers and Colourists.
Subscribe to our mailing list and stay up-to-date with news and developments in ITMA and the textile and garment industry.